FES at Bauma Germany 2025| Join to Discuss Common Challenges in Foundation Auger Drilling and FES Solutions
Bauma Exhibition Highlights: FES Foundation Drilling Tools Attract Attention
At the 2025 Bauma exhibition in Munich, Germany, the FES booth became a gathering point for foundation construction professionals. We showcased a comprehensive range of high-quality foundation drilling tools, including various specifications of drilling buckets, drilling augers, CFA (continuous flight auger) and drilling teeth. These precision-engineered foundation tools attracted numerous visitors who stopped by for consultations.
On the second day of the exhibition, an experienced contractor from Eastern Europe spent nearly an hour at our booth. Despite his 20+ years in the foundation engineering field, he candidly shared that his team still faces numerous challenging construction issues. "Technology advances, but so do the problems," he remarked. This contractor engaged in an in-depth conversation with our Technical Director, Mr. Ma, sharing the practical difficulties and industry pain points his team encounters during auger drilling operations.
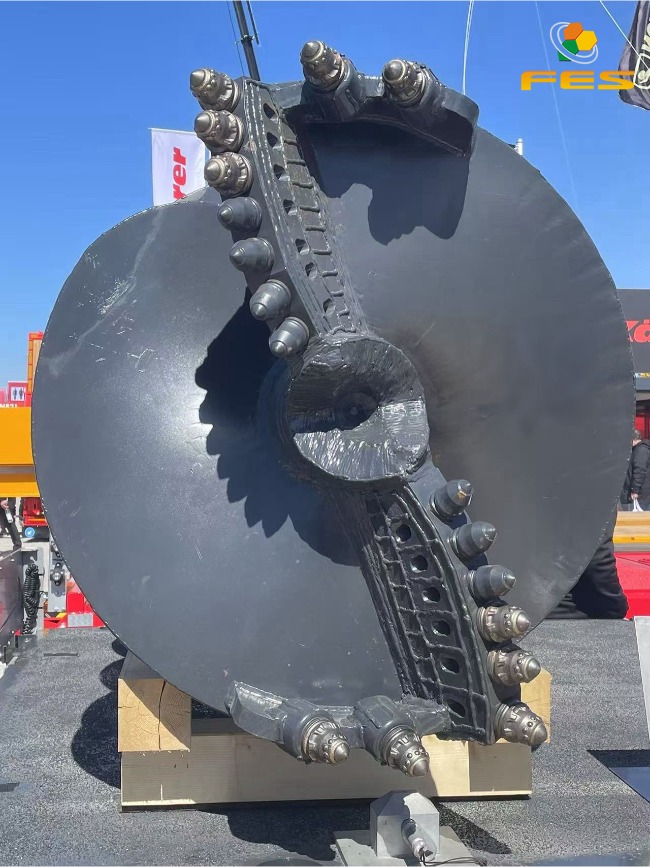
Today, we're sharing the valuable insights from this exchange, hoping to provide valuable reference for more foundation drilling engineering professionals.
If you're currently attending Bauma Germany—or planning to visit this week—we'd love to connect!
FES is offering one-on-one on-site consultations for drilling contractors and tooling distributors. Whether you're exploring new solutions or facing specific foundation drilling challenges, our team is here to help.
We'll be in Germany from April 7 to 13 — feel free to reach out and schedule a meeting!
Message us now for a quote or consultation
Email: rebeccayang@ougangroup.com
WhatsApp: +8613868064820
Common Foundation Auger Drilling Challenges and Solutions
In modern foundation engineering, augers are widely utilized for their efficiency and adaptability. However, even experienced teams frequently encounter technical challenges during construction that can lead to project delays, increased costs, and equipment damage. Based on our in-depth discussions with clients at the Bauma exhibition, here are five common issues and how FES provides innovative solutions through superior design and craftsmanship.
Challenge 1: Low Drilling Efficiency - When Every Minute Counts
Field Case: An Eastern European client shared their experience on a commercial building project. Their team was using traditional augers in mixed clay and gravel layers, achieving drilling speeds 50% slower than projected, severely impacting the overall construction schedule. Replacing the drill head provided some improvement, but efficiency remained suboptimal.
Possible Causes:
- Worn or dulled teeth with reduced cutting capability
- Complex geological conditions with inappropriate auger and teeth selection
- Insufficient drilling rig power output
FES Solution: Our engineering team has developed specialized augers and teeth based on decades of field experience:
- Different Auger Types:
Single-cut augers for clay, sand, and partially weathered rock;
Double-cut augers for dense sand, gravel, and weathered rock;
Single-flight augers for soft soil, clay, and silt;
Double-flight augers for medium-dense sand and clay;
Soil augers specifically designed for clay, silt, and loose sand;
Rock augers engineered for hard soil and weathered rock formations;
Straight augers optimized for clay and sand conditions;
Progressive augers for medium-hard soil, clay, and dense sand.
- Specialized Teeth Options:
Bullet teeth for hard soil, cobble layers, and weathered rock
Flat teeth for clay, sand, and soft rock formations
- Our carbide teeth and alloy steel are made from high-strength materials, with carbide teeth offering up to 120MPa hardness and alloy steel having a yield strength greater than 835MPa. We also offer an optional 65Mn wear plate with a surface hardness of around HB280, and an alloy steel forged teeth plate with a hardness of HRC28-30 after heat treatment. Additionally, high-hardness, wear-resistant welding wire with a surface hardness above HRC55 further enhances durability.
- The unique spiral angle design and tooth arrangement significantly enhance soil discharge efficiency in loose layers.
- Most importantly, beyond traditional welded options, we also provide an integral cast Kelly box for high-strength applications or continuous operations, ensuring maximum durability and performance.
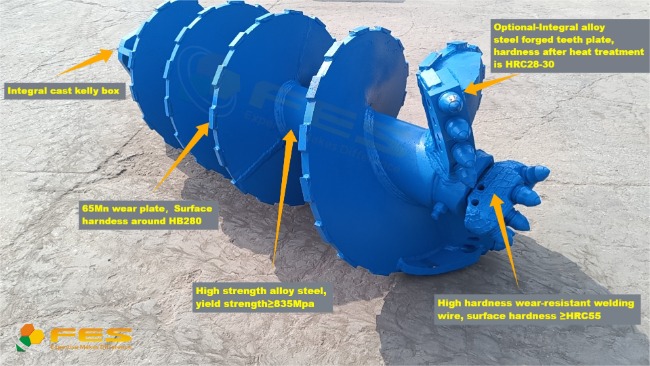
Challenge 2: Severe Vibration and Abnormal Noise - Threatening Equipment Lifespan and Operation Safety
Field Case: A Middle Eastern client described problems encountered at a site with alternating soft and hard soil layers. Their conventional drilling tools produced severe vibrations when transitioning between layers of different hardness, making control difficult and causing connection points to loosen. Another client reported abnormal noise after approximately 200 operating hours, which was initially ignored. Two weeks later, the gearbox completely failed, resulting in expensive repairs, project delays, and damaged client relationships.
Possible Causes of Vibration:
- Uneven weight distribution causing rotational imbalance
- Poorly designed connection points with excessive clearance
- Unstable contact between drilling tools and soil layers
- Insufficient vibration dampening in the drilling rig itself
Causes of Abnormal Noise:
- Worn or damaged gears
- Bearings lacking lubrication or already damaged
- Loose connection points causing metal-on-metal impact
- Poor alignment in the transmission system
FES Solution: Our foundation augers employ precision manufacturing techniques:
- High-precision design with symmetrical blades, balanced tooth distribution, and precision welding, with each tool undergoing dynamic balance testing before leaving the factory.
- Tight tolerance control between the Kelly box and connection sleeve to enhance connection stability and reduce wobbling, deflection, and noise.
- High-strength steel materials and integral heat treatment processes that improve overall strength and toughness while reducing deformation risk
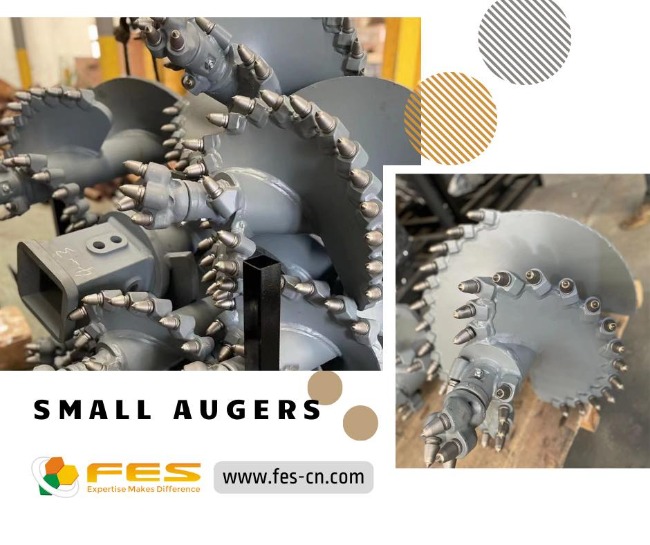
Challenge 3: Auger Getting Stuck - A Project Progress Nightmare
Field Case: At the Bauma exhibition, a French client described a harrowing experience during a residential development project. At a depth of 12 meters, the drilling tool suddenly became stuck, with conventional methods proving ineffective for extraction. They ultimately had to employ additional equipment and manpower to resolve the situation.
Possible Causes:
- Sudden soil layer collapse burying the drilling tool
- Drill auger trapped in unforeseen large rocks or rock layers
- Excessive drilling speed causing soil over-compaction
- Tool design lacking capability to handle complex geological conditions
FES Solution: We recommend clients equip their drilling rigs with high-torque power heads to handle extreme situations, while also offering product solutions. Our straight rock auger is specifically designed for hard rock applications, providing superior rock-breaking efficiency and making it easier to free stuck drill heads by breaking through the surrounding formation.
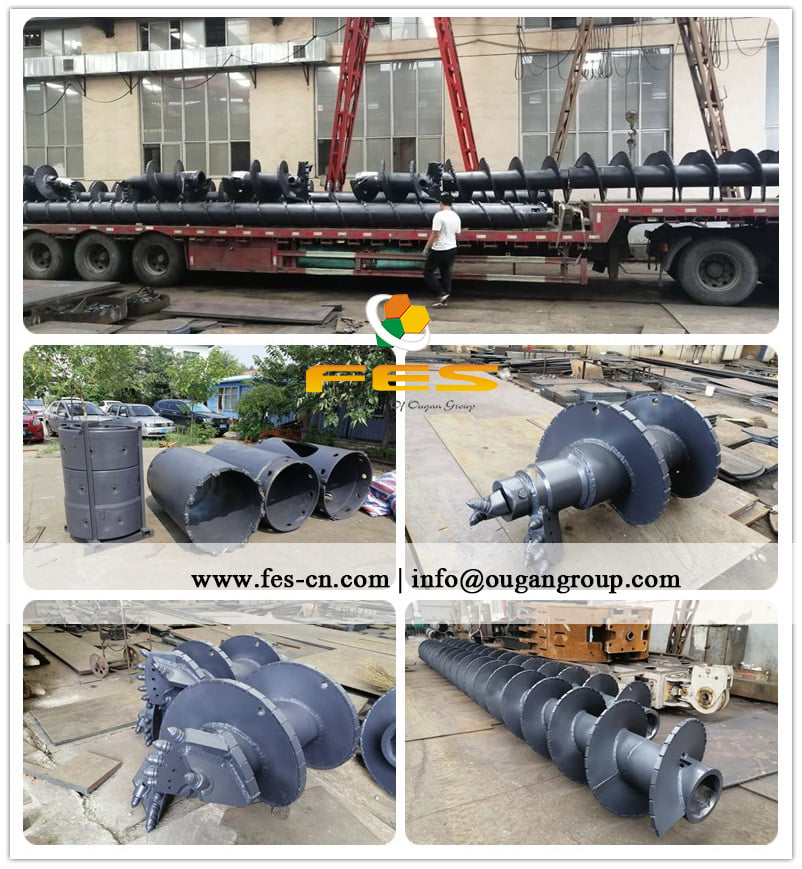
Profound Insights from Technical Exchanges at Bauma
During the week-long Bauma exhibition, the FES technical team engaged in in-depth discussions with professionals from around the world. We not only addressed client questions about how operational practices and geological characteristics affect construction outcomes but also detailed our innovative product solutions.
These exchanges reaffirmed our design philosophy: truly exceptional foundation drilling tools must not only deliver outstanding performance but also effectively address the various challenges and unexpected situations encountered in real-world engineering projects. The FES foundation auger product line embodies this philosophy, integrating advanced materials science, precision manufacturing techniques, and practical field experience to provide reliable, efficient, and safe drilling solutions for global clients.
Conclusion
FES foundation auger products are designed to withstand diverse working conditions while offering customized support. We understand that each engineering project presents unique challenges, and our technical team stands ready to provide expert advice.
Schedule your meeting now for more expert advice!
Email: rebeccayang@ougangroup.com
Phone/WhatsApp: +8613868064820